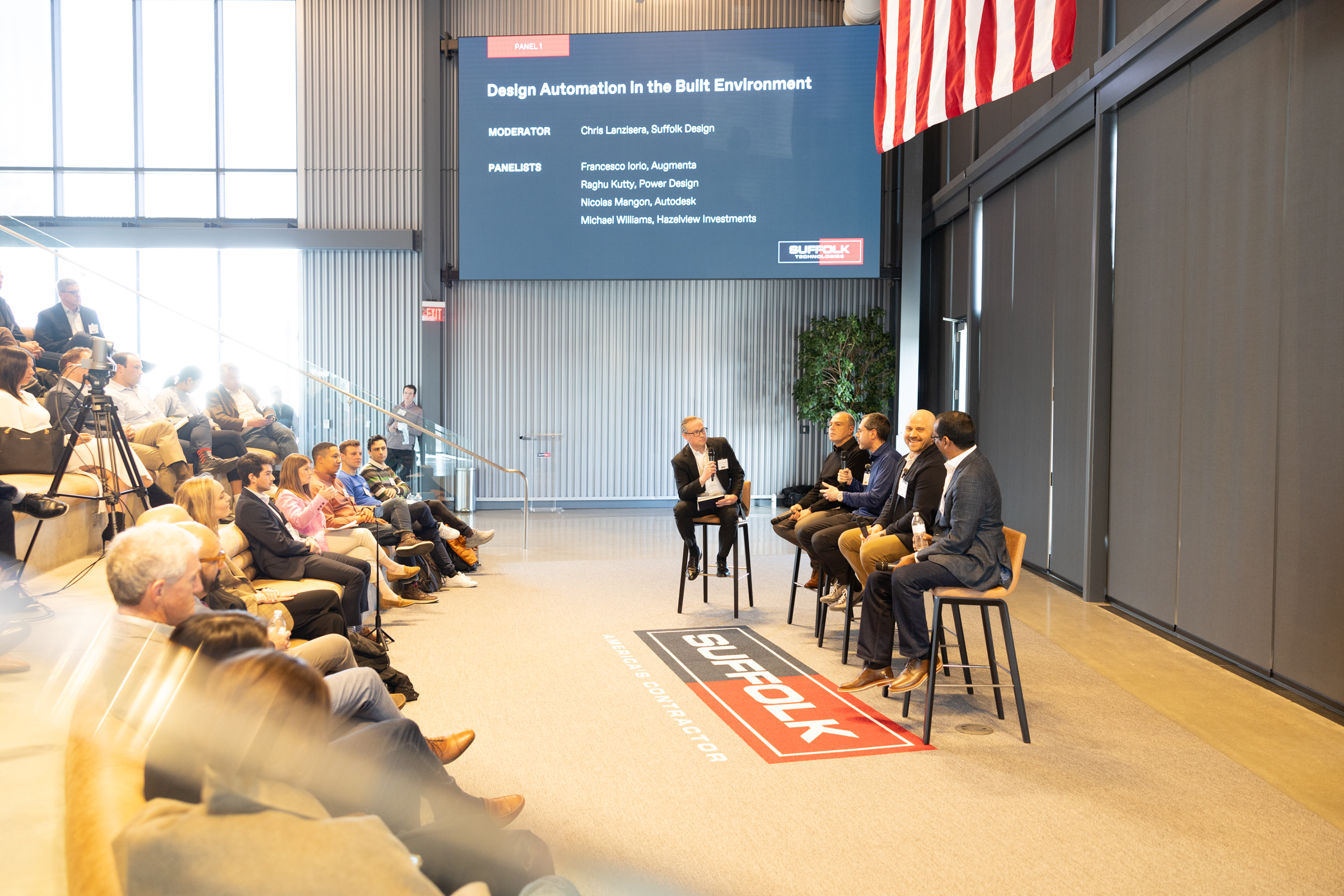
The November 2022 release of ChatGPT sent shockwaves through every industry, including the built environment. Everyone could easily see for themselves just how powerful generative artificial intelligence (AI) had become. And if AI developers’ predictions about scaling laws are correct, AI will become exponentially more capable not in the next decade, but just the next couple of years.
In Architecture, Engineering and Construction (AEC) specifically, AI may catalyze a wave of innovation for an industry whose tools have not changed much over the last decade. CAD, for example, emerged four decades ago. Revit introduced BIM 20 years ago, and while BIM did begin taking advantage of the cloud in the last decade to create Connected BIM, as Nicolas Mangon, VP AEC Strategy at Autodesk, notes, “Nothing much has changed in the last decade.”
Mangon was one of the speakers and panelists at a half-day summit that Suffolk Technologies recently hosted titled: AI + Design in the Built Environment. This event brought together thought leaders from established tech companies and startups working at the edge of AI to have a real discussion alongside industry practitioners, from developers and owners to engineers, architects, and builders about the key challenges of AI adoption for design and construction. The stacked panels discussed the bottlenecks in the status quo, current applications of AI in AEC, and requirements to enable AI.
The problem with the AEC status quo
The increasing cost of design and construction is a huge challenge. For instance, the costs of designing, obtaining permits, and constructing new buildings have grown to the point that it’s becoming more common for projects to cost more than they are worth. These projects are also rife with delay. More than 1 in 5 (22.7%) projects are delivered more than 250 days late, and more than 1 in 8 (13.4%) are delayed by at least a year.
Part of the problem is that much of the design process is manual and repetitive. When designers themselves make mistakes, they’re hard to catch and fix. And when any of the various parties involved in designing a building makes changes to plans, those changes don’t always cascade down to the final plans in the builders’ hands. These changes can in turn cause errors and misunderstandings that require costly, time-consuming rework.
Another issue is the lack of shared information among the many parties that must collaborate to design and build a new building. There is a strong incentive to successfully complete the project, but not to share analytical data on projects over time. People, companies, and teams come together for two to three years and then never work in the same framework again. After all, while collaborators are giving it their all for years to deliver a building, once it’s done, they might be competitors on a future bid. It’s not that these companies don’t want to play nice and share, but the project-based nature of construction disincentivizes data sharing.
Additionally, even when the various parties do want to share data, doing so is very difficult, due to incompatible systems and lack of data standards. The files that need to be shared across parties are also typically very large, further encumbering shareability and collaboration. Dashboards such as Power BI have helped the industry get more transparency, but that’s just the tip of an iceberg and there’s still a long way to go.
Until the data problem is solved, the industry will continue to suffer from lack of transparency between designers, owners, and builders. And, unfortunately, this situation presents significant challenges accumulating exactly the kind of long-term, project-to-project data that advanced technologies such as AI need to uncover insights and make predictions that could reduce costs and accelerate time to delivery.
AI applications in AEC
While there are challenges with applying AI to the AEC industry today, there are many areas where the latest AI tools can have a meaningful impact on the industry.
Intelligent and Automated Design Solutions
We are not yet — and may never be — at a point where AI can properly design a building start to finish. But it has become clear that AI can provide meaningful assistance to designers. For instance, AI could analyze a design and produce a manifest of all the required materials or, even better, suggest design or material changes that could save money without significantly changing the vision for the building. They could also train on prior designs to provide components such as a bathroom or office. Already, solutions exist that will scan the design for code and logic errors, such as walls that don’t align or violate building codes.
“Error detection is a big benefit,” says Jim Dray, principal and CIO at Thornton Tomasetti, an engineering firm that optimizes the design and performance of structures, materials and systems in AEC. ”I’d love to run an expert system on a BIM that says, ‘These 12 things don’t look likely. A human should check it out.’”
Model Sharing
AI can also help reduce the size of models and make it easier to share models and other information across stakeholders, because the problem is not just one of will. It’s also a technology problem, and AI can assist with making sharing much easier.
Gryps, for example, is building an AI-powered platform that finds and makes data easily accessible to AEC stakeholders in a secure manner. And Speckle is building an AI-powered, open-source platform that enables AEC organizations to manage, share and easily access 3D design data in CAD/BIM, parametric design, and even custom tools. Companies can extract and exchange data in real time from AEC apps, curate and share objects instead of giant binary blobs of data and collaborate across teams and disciplines. Thornton Tomasetti is also addressing this challenge with Konstru, a startup that spun out of its internal accelerator, TTWiiN.
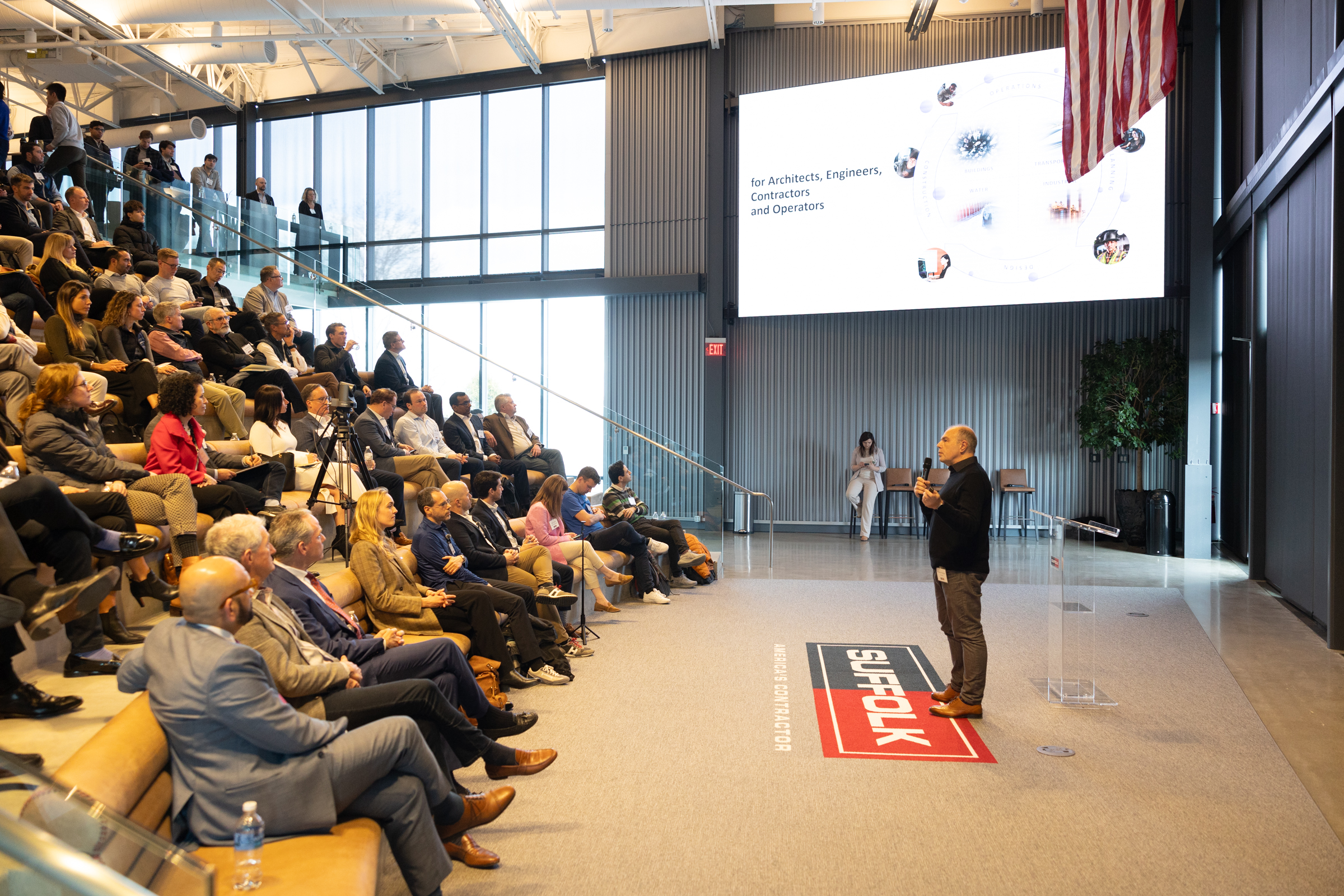
Digital Twins
To Mangon at Autodesk, digital twin is one of the more powerful capabilities AI can enable. A digital twin creates a virtual model of the project which can then be used to assess how different events will affect scheduling, manufacturing plans and even the building itself. Changes, such as a delay in the delivery of key materials, can be run through the digital twin to see exactly how they will affect cost and schedule, along with any unexpected impacts on other aspects of the building. In an industry that is perpetually risk averse, enabling consideration of disparate data sources can help assess and manage risk proactively.
“BIM was sold as a holy grail where everything in the field can be done in the office, but getting that model to be accurate is painful, especially for subs,” said Raghu Kutty, CIO at Power Design, a company that provides multi-trade design-build services for electrical, mechanical, plumbing, and systems technologies. “I want construction tech companies to make it possible for changes to flow through to a BIM model with everything updated in real time.” AI can also assist with proliferating those changes across several stakeholders, without the need for duplicative data tracking and input.
Efficient Design
Modular design is slowly creeping in as a model for creating buildings in the industry, with prefabricated components coming to use on projects. Modular design was created in part to address all the complexity and dysfunctionality in design by simplifying the design process and driving standardization. AI could help automate the customized workflows in such a way to allow more customization in design itself, while simultaneously making the process more efficient, which could reduce the need for modular approaches.
For instance, the repetitive components of a design (bathrooms, offices, etc.) can be componentized and slotted in automatically during the design phase, which accelerates the process and saves designers and trades from doing repetitive, boring work. AI can adjust and optimize each component to provide more efficient use of standardized materials and analyze past building designs to optimize new designs. In this way, designers and trades can free up their time to design more unique aspects of buildings, rather than focus on repetitive details.
Environmental Reporting
Environmental reporting is another area in which AI support will likely prove invaluable. Embodied carbon reporting is becoming a standard requirement in many states and cities, but even where local laws don’t apply, owners such as Google and Meta expect it. In fact, pressure to provide environmental data on buildings could very well be the factor that finally persuades the industry to lower its data barriers and become more transparent.
Requirements to enable AI
The promise of AI to increase the efficiency and accuracy of the design process is enormous, but enabling AI requires a lot of data, which is a challenge for an industry where stakeholders have been traditionally very reluctant to share.
”The integrated design process of the last 10 years isn’t working. Getting data on a technical side works, but we’re so siloed and resistance at one level messes up all the others,” said Michael Williams, Managing Partner at Hazelview Investments, an investor, owner and manager of real estate investments.
AEC is an extremely competitive business, and this year’s partner could be next year’s competitor. Understandably, people don’t want to share data that could be used to gain a competitive advantage over them. But there are ways to share data that don’t compromise proprietary information on internal best practices and methodologies.
The usage of synthetic data, for example, is an avenue pursued by multiple technology companies to train machine learning models in circumstances where real data is difficult and/or very expensive to obtain. Synthetic data are artificially created sets of data created by algorithms that contain accurate representations of the salient features and characteristics of real design data. It could provide a partial solution to the data sharing problem. According to Francesco Iorio, CEO of Augmenta, a company that provides automated design solutions for MEP, synthetic data provides value while also ensuring privacy and avoiding compromising proprietary information.
Synthetic data is already in use for training AI in situations where it’s difficult to collect a critical mass of real data. In fact, Gartner predicted in 2023 that by 2024, “60% of data for AI will be synthetic to simulate reality, future scenarios and derisk AI.” For example, Amazon’s Alexa AI system was partially trained on synthetic data for its natural language understanding (NLU) system, and financial giants such as J.P. Morgan have used it to train fraud detection models. Given our industry’s challenges in sharing data, synthetic data could provide a way forward for AI until data sharing becomes easier and more commonplace.
“We can go a long way with synthetic data,” Iorio says. “Project data can be used for other purposes, like unearthing some unwritten rules that pertain to individual firms, and that may remain so. People don’t necessarily have to give up proprietary secrets.”
Even if the industry does begin to share data though, the question is how. The giants of the industry are just now starting to create interoperability standards, which should aid in sharing data sets across different design tools. The lack of a standard has made building data sharing solutions that work with multiple applications and platforms extremely difficult. Companies like Speckle help further address these challenges by creating an open-source environment for model sharing, and creating a community of like-minded individuals that encourage collaboration.
“AI can help companies share only data related to the specific project. Ultimately, though, growing incentives to share will change the industry’s approach,” notes Jim Dray. “Eventually, those firms that share data will gain competitive advantages over those that do not, and, once it becomes apparent that transparency increases profitability, the data floodgates will finally open.”
“This change will happen because people will make more money by pooling data,” Dray added. “Capitalism will be the driver.”
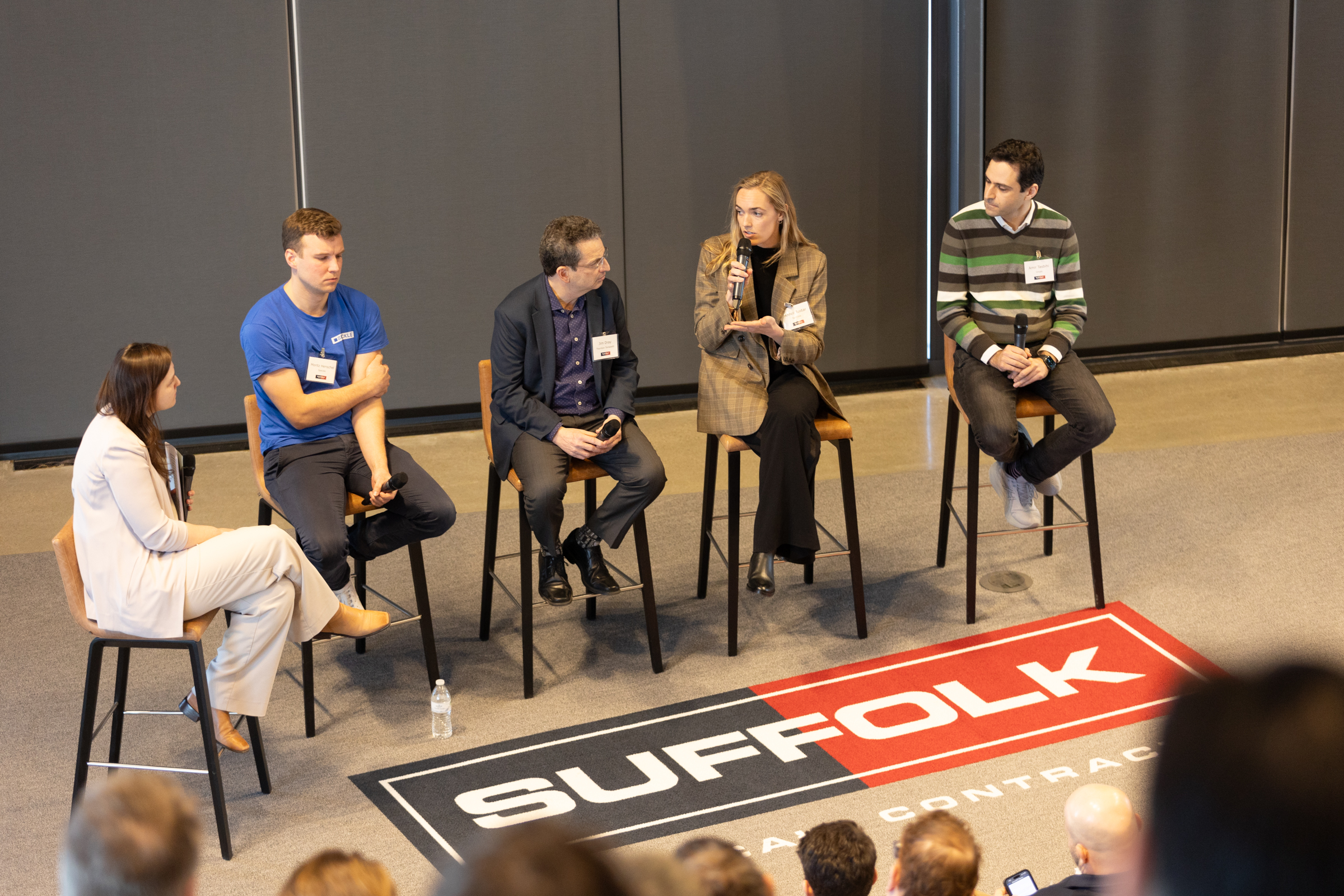
Sustainability is another force pushing the industry to share data. In fact, Anneli Tostar, CEO of Tangible, a company that helps real estate developers and owners manage and reduce emissions from building materials, says that “sustainability is the Trojan Horse for collaboration. This data needs to be legible by multiple stakeholders.” Tostar described how AI can facilitate accurate environmental reporting that shows auditors exactly how figures were determined. As owners and regulators increasingly expect to see environmental impact data in their buildings, project partners will need to share data to comply.
While capitalism and sustainability are two great forces that may start aligning incentives among a fragmented set of stakeholders, ultimately, it may be up to owners to set standards and push for data access and data sharing. As Williams notes, owners are in the right position to ask and receive information from all parties during the building process. But, if owners are to understand what data they already have and what they’re still missing, they’ll need some technological help. As Amir Tashibi, CTO at Gryps, said “Fragmentation is here to stay. Owners have multiple systems, and they’ll stay like that for the most part.” His company provides solutions that enable AEC companies to aggregate and access data from disparate systems so it can be analyzed.
AI has the potential to propel AEC forward toward previously unthinkable gains in efficiency, accuracy and profitability, as the speakers at AI + Design in the Built Environment event demonstrated. But realizing this dream will require the industry to shed its fears of sharing information and embrace new technologies that will facilitate data transparency. Forward thinking firms that begin collaborating and sharing data now, before business and regulatory pressures make it impossible to do business without transparency, will gain significant advantages that will set them apart and ahead of competition.
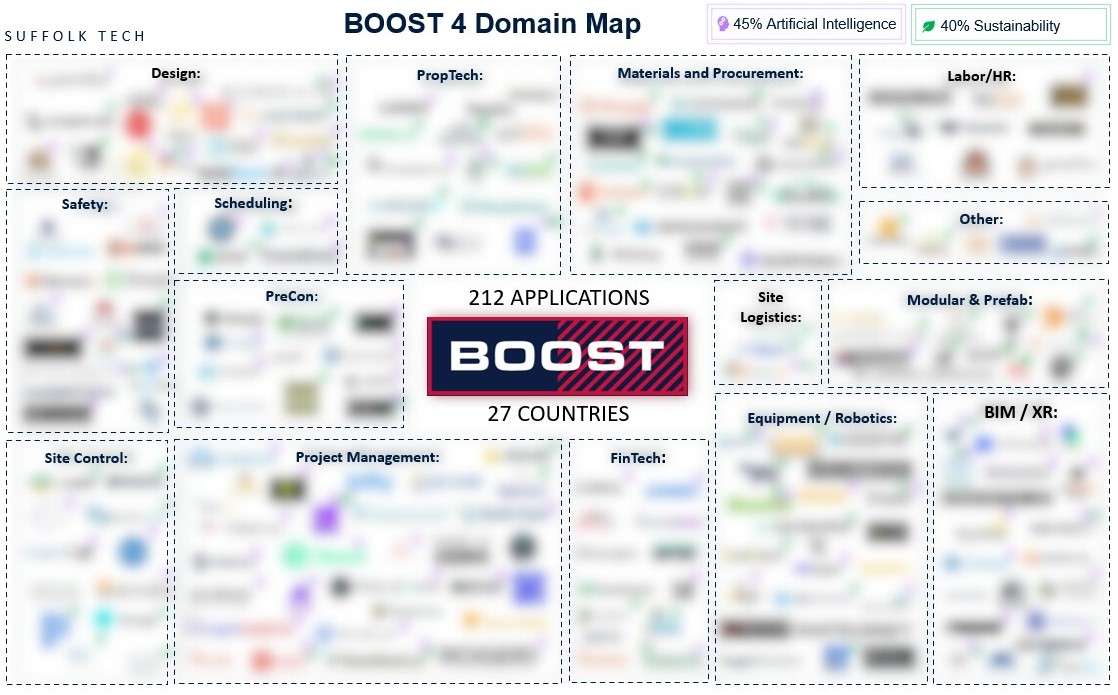
About BOOST:
Every year, Suffolk Technologies welcomes the biggest innovators in the Architecture, Engineering, Construction, and Operation (AECO) space for an intense 6-week accelerator program, exposing early-stage entrepreneurs to every facet and detail of the built environment ecosystem. This year, in our fourth edition of the program, we selected seven companies and have been excited to see them progress through challenges they face as founders and technologists in the built world.
BOOST 4 received 200+ applications from 27 countries this year, more than twice the number of applications than when the program started in 2020. The applicants touched on all aspects of the built environment, with a strong showing across six key themes including artificial intelligence, supply chain efficiency, informed sustainability, field-focused digitization, design optimization, and workforce productivity.
The seven companies selected to participant in this year’s cohort, AGORUS, Emidat, Exodigo, Hammr, KayaAI, Sitelink, and Trunk Tools, are building solutions across these six themes and improving their products and go-to-market strategies with the support of Suffolk Technologies and our 22 industry partners.
Talk to me about the themes…
Artificial Intelligence
The question is not if artificial intelligence (AI) can help change the way we build, but rather how it will affect our industry. AI has already begun to transform our industry significantly – new technologies can automate tasks such as checking 2D design documentation for discrepancies, ensuring code compliance, and identifying coordination clashes. Several emerging technologies are using image recognition to automate laborious tasks such as facade inspections, progress tracking, and surveying. In fact, 45% of BOOST 4 applicants, and almost all chosen participants, note AI as a core feature of their products.
Having said that, AI is unlikely to replace construction professionals anytime soon. Many industry reports rank construction at the bottom of the pack when it comes to AI impact1 and, while we believe this impact will be large, we foresee AI working alongside construction professionals to reduce drudgery and drive productivity instead of displacing workers. AI will serve as a co-pilot to automate back-office tasks, prompt contractually driven actions during a project, and easily serve up information when and where it is needed. The differentiation for AI-enabled applications will be centered around the details and timing of inputs and outputs – AI layers that easily integrate into existing systems and processes will be the quickest and easiest for the industry to adopt.
Supply Chain Efficiency
Construction input costs have increased by an average of 26% in 2021 and 2022 due to factors that include lack of transparency throughout the supply chain and delays caused by macroeconomic disruptions such as COVID-192. With limited options available for reducing the cost of raw materials, construction firms are turning to new technologies to help them track the movement of materials, monitor inventory levels, optimize procurement processes, and reduce material waste, ultimately leading to smoother operations and cost savings. For example, AGORUS is utilizing AI-enabled software and robotics to precisely cut and assemble customized timber members of buildings to be installed rapidly on the jobsite, ultimately reducing assembly time, and mitigating costly waste.
We believe the lack of visibility throughout the supply chain can be addressed with technological solutions. General contractors and developers can increasingly leverage software solutions to capitalize on once hard-to-find purchasing power and begin purchasing larger ticket items, such as electrical and mechanical equipment. Other solutions are empowering the offsite tracking and management of materials. For instance, KayaAI has been building tools to integrate AI-driven visibility into our ecosystems’ pre-existing processes and increase lead time visibility on construction projects.
Informed Sustainability
In an era when sustainable business practices are increasingly becoming a competitive advantage, construction firms are exploring how they can address sustainability challenges and transparently communicate their impact. No matter what path firms choose, the first step will be measuring and reporting on various sustainability metrics to demonstrate commitment to sustainable development and meet the demands of stakeholders, regulators, and the broader community. Helping companies navigate the first step are companies such as Emidat. Emidat helps building material manufacturers easily create and distribute environmental product declarations (EPDs), the foundational impact data for embodied carbon stakeholders can leverage to make informed decisions.
The ability to establish industry-wide sustainability baselines will drive the implementation of new processes and methodologies that can power continuous improvements that reduce the built world’s environmental footprint. Metadata collection and aggregation are critical in the coming years as the U.S. slowly, but surely, adopts and pushes for increased reporting and visibility into the materials and processes used to build. There are two key challenges that this new wave of regulations will present for commercial real estate owners: 1) Getting access to reliable and trusted data, which is most often found at the source (such as manufacturers and producers), but also the most difficult to access, and 2) Helping decision-makers across the value chain prioritize the best ROI solutions when it comes to reducing their impact.
Field-focused Digitization
We are excited to increasingly observe technology tools catching hold with a ‘bottom up’ approach, where adoption starts with superintendents and project managers, rather than a centralized innovation team. The ‘top down’ approach to design, project management, building information model (BIM) creation, and reporting has enabled the industry to set standards, adopt new technologies, enforce consistency, ensure back-office efficiency, and drive continuous improvement in enterprise-wide programs and standard operating procedures. In contrast, the ‘bottom up’ adoption promises to streamline workflows and increase productivity in the field, empower frontline professionals to address challenges with data at their fingertips, and address root causes of project delays and cost overruns.
To reap the full benefits of a streamlined, real-time workflow, the perpetual dissonance between BIM and field updates needs to be solved – a gap Sitelink is trying to address with their AR-powered field app. Their solution was built to enhance collaboration for construction teams by bringing BIM to the jobsite. This explosion of field technology coincides with demographic trends we expect to gain momentum in the coming decade. As more than half of the current labor force phases out of the skilled trades, we expect tech-enabled efficiency gains to become more critical and demanded by the workforce, incentivizing network effects rather than forcing outdated tools on individuals in the field.
Design Optimization
As building designs and code complexity increase, optimizing the time that it takes to create design and construction documents in 2D, and 3D has become a focus for design and construction professionals – and a great seeding ground of many tech companies. With added complexity, the time and effort required from professionals to generate a valid, code-compliant set of drawings has increased tremendously. One way to accelerate the production of these documents is assisting with reality capture of existing site conditions, which helps to not only speed up the design process, but also avoids unexpected problems in the future. This has become especially relevant for project starts. Having accurate information from the outset reduces requests for information in-field, minimizes rework, and streamlines the schedule. Sub-surface mapping solutions, such as the one being developed by Exodigo, can provide a clear picture of the underground, informing partners where to design and build safely with a high level of predictability, and doing so faster and more efficiently than existing intrusive methods.
There are rich opportunities for optimizing design beyond project starts as well. Other solutions focus on AI and automation of certain repetitive design tasks. Today, designs are often created from scratch, rather than leveraging institutional knowledge accumulated through previous projects. Thankfully, pulling in previous details and specs from similar projects from the past is becoming easier with today’s tools, helping architects be more productive with their time. Furthermore, the ability for multiple architects to simultaneously collaborate on a drawing set has circumvented the need for downloading or sharing large file formats, avoiding previously disjointed workflows. With so many components to design, such as balancing aesthetic considerations with functionality, sustainability, and cost-efficiency, technologies that enable a more informed, collaborative design process can meaningfully affect change in the industry.
Workforce Productivity
Workforce productivity stands at the core of the AECO industry’s success and profitability. In an environment where the cost of materials and labor are increasing, optimizing the performance of the construction workforce is critical. From skilled laborers to engineers to project managers to back-office functional roles, harnessing the full potential of human resources is not only essential for meeting deadlines and staying within budget, but also for ensuring the safety and quality of construction projects.
Many startups are addressing issues of productivity in the AECO space. For example, Hammr identified an urgent need among SMB contractors through their social media community (the “Bred to Build” podcast) and addressed those needs by building a tool for automating back-office processes. Other early-stage startups are looking at ways to improve workforce productivity by focusing on the field, solving challenges related to training and upskilling the workforce or aligning pay incentives on the jobsite. Trunk Tools addresses the skilled labor shortage in construction by creating easy to use tools for the deskless workforce, including AI-driven superintendent bots that help answer on-site questions and task-based incentives to drive productivity. With better tools in the field and in the back-office, productivity of the jobsite will increase over time.
What Comes Next
The seven startups selected to participate in the BOOST 4 program spent six weeks working with Suffolk Technologies throughout October and November. The BOOST program allowed them to explore and define new use cases within AECO and refine their products and go-to-market strategies. More than half of all BOOST participants have piloted their technology on Suffolk jobsites and many are also exploring pilots with our Operating Partners including Axiom Builders, Holcim, Sellen Construction, and Century Drywall.
If you are interested in learning more about the BOOST program or becoming involved in the future, please reach out to [email protected] and a member of our team will be in touch.
This year, BOOST is presented in partnership with 22 industry partners including Group Amana, Autodesk, ARCO Murray, Axiom Builders, Century Drywall, Feldman Geospatial, Gunderson Dettmer, Holcim, JLL Spark, Liberty, Liberty Mutual, LMRE, McCusker-Gill, The Martin Trust Center for MIT Entrepreneurship, Moog Construction, Procore, Sellen Construction, Suffolk, Suffolk Design, Swire Properties, Thornton Tomasetti, and Zwick Construction.
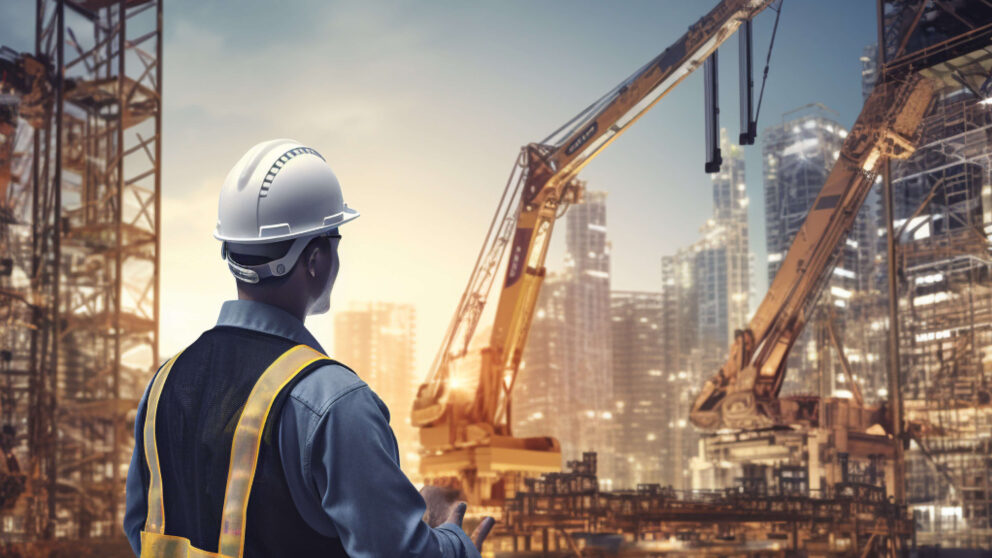
We’ll be blunt. Construction has a huge productivity problem. In fact, it’s bigger than you probably imagine, because construction isn’t just failing to keep up with the gains of the overall U.S. labor force, which have averaged about 2.1% annually since 1994. No, construction’s productivity has actually declined from 1970 to 2020 by 40%, according to the National Bureau for Economic Research. And this productivity problem isn’t just an issue for construction — it’s a problem for the entire global economy. Construction directly and indirectly accounts for 13% of the world’s GDP.
Compounding the productivity problem, construction is also suffering from a massive — and likely long-term — labor shortage. To keep up with projected demand, the industry will need to attract an additional 546,000 workers on top of its usual pace of hiring, according to research from the Associated Builders & Contractors. Unfortunately, unless conditions undergo a rapid turnaround, that’s unlikely to happen. Last year, construction averaged 390,000 job openings each month, which is the highest level since stats have been recorded for the industry.
Other industries such as manufacturing have been able to increase productivity, despite sizable challenges of their own. But in construction, we are only in the early stages of what will be a massive transformation.
Suffolk Tech sees AI and automation as the ultimate solution to the industry’s productivity challenges. With our new fund, we invest in solutions and leverage our platform to help rapidly scale the right solutions across the industry. We firmly believe that these technologies can help the industry reverse course to start seeing the kind of productivity growth other industries have experienced.
But, of course, our position begs the question: why is construction still relying on manual processes and technologies that are decades old? Is construction made up of a bunch of technology-hating Luddites?
A Low-Margin, High Risk Industry
The answer to that last question is easy: a strong and emphatic, “No.” Though the explanation why is a bit more complex…
First, it’s important to understand that construction is a high-risk, low-margin business. The typical net profit margin for engineering and construction is less than 3%. That’s comparable to commoditized industries such as grocery stores (2.1%), electronic components (4.1%) and auto parts (2.6%).
As for risk, construction has a ton. In manufacturing, for instance, the environment is largely closed, and conditions inside a facility are controllable. Processes are also highly repeatable, because manufacturers make the same product over and over, gaining efficiency. Construction, on the other hand, is largely outdoors, subject to unpredictable weather and ground conditions. Each building is different, so processes must change from project to project. So, many of the factors that determine the success or failure of a project are completely out of a single company’s control.
Additionally, in construction, time is extremely precious. Late projects incur penalties that can easily wipe away profits, and given how much leverage is involved, owners need to start seeing revenue from their investments as soon as possible. A failed or late project can tie up all the stakeholders in years of costly lawsuits and red ink.
The fact is, in a high-risk environment with low margins and aggressive deadlines, the appetite for changing processes and adopting new technologies historically has been understandably low. Why take a chance on a new technology that could fail and put the entire project at risk? Construction managers see far less risk remaining with the status quo. Nevertheless, the pressures to deliver more buildings, faster, cheaper, and more sustainably are turning many stakeholders towards seeking better technological solutions to previously manual and slow processes.
Near-Term Opportunities for Automation and AI in Construction
To succeed, technology entrepreneurs must first understand the unique challenges of the industry. But that’s just the start. Their solutions must also be:
- Able to deliver rapid ROI: If a construction organization is going to take the risk of incorporating new technology into their workflows, the benefit needs to be significant and immediate.
- Easy to use: In construction, people are extremely busy and working to aggressive schedules. They simply do not have time to learn how to use a complicated UI.
- Mature: While there are construction organizations like Suffolk Construction that are eager to help entrepreneurs develop and improve their solutions, the market at large expects technologies to be ready for prime time.
- Designed with construction’s unique challenges specifically in mind: If horizontally-oriented, general-purpose technology solutions would work for construction, they would have adopted them.
Now that we’ve described the traits a technology solution needs to have for construction, let’s dive a bit deeper into automation and AI, specifically. Generally speaking, there are two spheres where it’s applicable. The first is physical automation, which includes equipment, labor and building management. The other is digital automation for use cases such as data analytics, model-driven design, project management, and others.
There are a multitude of potential use cases under each sphere, but here are a handful of the ones we believe have big near-term potential.
AI-Assisted Design: Currently, the processes for building models, plans, and designs are mostly manual and, probably surprising to many, even paper-based. It’s slow with a high risk of introducing human error. Contractors, for instance, spend weeks creating detailed models prior to build out. It’s a reactive process with very slow iterations, and decisions are often based on gut feelings. A good example of a company that is transforming how trades can leverage design to improve their process is Augmenta.
Augmenta uses AI to create electrical (and eventually mechanical and plumbing) designs within minutes vs months. Their designs are also tied to the bill of materials, which makes estimating fast and accurate. Considering it can take up to two months to create these designs manually with frequent changes required, employing this tool presents a game-changing advantage. Currently, Augmenta can create designs for fully detailed, code compliant, and constructible electrical raceway systems. In the near future, the company will add capabilities for creating plumbing, mechanical, and structural designs.
Data Analytics and RPA (robotic process automation): Capturing and analyzing data about a jobsite is a huge challenge. Manual data entry is, of course, slow and error prone, and manually captured images are often not comprehensive enough and can’t be analyzed at scale by humans. OpenSpace uses machine vision and AI to provide a complete, up-to-date digital view of the jobsite from 360 degree images captured from a camera mounted on a worker’s hard hat or, if available, an autonomous robot.
OpenSpace’s AI goes well beyond creating a digital jobsite view. It can show progress over time, and compare the actual site to a model to identify discrepancies early, when they are less expensive and easier to address. Contractors can also use the solution to simplify communications about scope of work and to document changes.
Robotics: If robots can perform tasks – especially dangerous ones – that are ordinarily completed by humans, they can help alleviate the labor crunch while improving safety, accuracy, and productivity. But the construction environment is super challenging for robots. In manufacturing, robots are ubiquitous, but factory floors are very different from construction jobsites, which are unstructured and always changing. Robots can’t work in isolation; they have to work alongside human workers safely and effectively. They must also be rugged enough to function in bitter cold and scorching heat, braving dust, standing water, uneven floors, and other hazards.
In the last decade, however, robotics has seen tremendous advancements, especially in their ability to move autonomously and collaborate with both humans and other robots. As a result, we’re starting to see young companies roll out robotics solutions designed specifically for construction.
Rugged Robotics, for example, replaces the slow and manual process of field layout with an autonomous robot that marks architectural and engineering (A/E) designs directly onto unfinished floors. It’s faster, more accurate and less expensive than marking floors manually.
Another company, Canvas, makes a worker-controlled robot that uses AI and machine vision to finish drywall 1.5x faster than a completely manual process. Incredibly, nearly every component for the robot is off-the-shelf, including the initial AI and machine vision algorithms, which goes to show just how much robotics and AI have advanced. With Canvas, one worker and a robot can do the work of an entire team faster and more consistently, which is a huge plus for an industry in the midst of a huge labor shortage. Plus, the Canvas robot creates very little dust, creating a healthier work environment with little to no cleanup afterwards.
Construction can see the same kind of productivity gains other industries have experienced through automation and AI, but these technology solutions must specifically address the unique challenges of the construction industry.
There’s still a lot of work to be done, even in getting things like baseline data to enable true AI and automation use cases (which we are also focused on solving with our focus on connected industry). But, one thing is clear, construction needs to change and new AI and automation tools can increase productivity across the industry. The idea of automated construction is not new (as can be seen from Villemard’s depiction of future of building in his 1910 image), but we see great potential on the horizon.
If you’re building a startup that addresses these or other pressing issues in the built environment, please reach out to our team.